Winches: A Comprehensive Guide to Top Types, Maintenance, Replacement and History
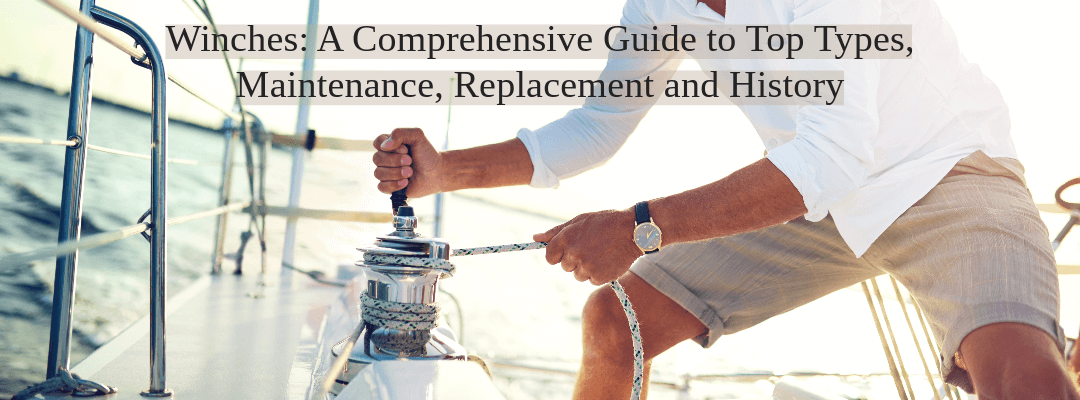
Overview of Winches
Winches and hoists have a rich history dating back to ancient civilizations, where simple pulley systems and ropes were used for lifting heavy objects. Over time, these essential tools have evolved into sophisticated devices that play pivotal roles in various industries, from construction to marine operations.
In this comprehensive guide, we will delve into the diverse world of winches. We'll start with an exploration of their history, tracing their journey from rudimentary systems to today's electric, hydraulic, and manual models. Understanding this history provides valuable insights into the continuous innovation and adaptation of these tools.
Maintenance is a key aspect of ensuring the longevity and safety of winches. We'll offer essential maintenance tips, including lubrication, inspection, and adherence to manufacturer recommendations. We'll also discuss the signs that indicate when maintenance is needed, such as unusual noises, slow movement, or cable wear and corrosion.
However, there are instances when maintenance alone may not suffice. That's when the decision to replace your winch becomes crucial. We'll provide guidance on recognizing signs that your equipment might need replacement, such as repeated breakdowns or outdated technology. Upgrading to a more efficient and capable model can significantly enhance productivity and safety.
Join us on this journey through the world of winches and hoists, where history, maintenance, and replacement intersect to ensure safe and efficient operations across a spectrum of industries.
The Top 10 Most Common Types of Winches, Accessories and their Applications
1. Electric Winches
Overview
Electric winches are the workhorses of the winch world. They are commonly used for vehicle recovery, especially in off-road situations where getting stuck is a real possibility. Electric winches are known for their reliability and ease of use.
Top 5 Applications
- Off-Road Adventures: Electric winches are a must-have for 4x4 enthusiasts. They can pull vehicles out of mud, snow, or tough terrain.
- Boat Trailer Loading: Electric winches make it effortless to load boats onto trailers, saving time and effort.
- ATV and UTV Applications: They are perfect for handling small vehicles like ATVs and UTVs.
- Construction Sites: Electric winches assist in lifting heavy materials and equipment to elevated positions.
- Emergency Towing: They come to the rescue when vehicles break down or need to be towed.
Typical Characteristics
- Load Limit: Varies from 2,000 lbs to 18,000 lbs
- Line Length: Up to 100 feet
- Power Source: Typically 12V or 24V DC
- Remote Control: Many models come with remote controls for convenient operation
2. Hydraulic Winches
Overview
Hydraulic winches are the go-to choice for heavy lifting and industrial applications. They are often used in construction and marine operations where immense pulling power is required. These winches are powered by hydraulic systems, making them capable of handling substantial loads with ease.
Top 5 Applications
- Marine and Shipping Industry: Hydraulic winches are used for lifting and lowering anchors, cargo, and other equipment on ships.
- Construction Sites: They excel in heavy-duty lifting tasks on construction sites, such as moving steel beams.
- Oil and Gas Sector: Hydraulic winches are crucial for offshore drilling operations.
- Mining Operations: They handle the extraction of heavy materials in mining processes.
- Towing and Recovery: Used in towing trucks and vehicles with substantial weight.
Typical Characteristics
- Load Limit: Ranges from 10,000 lbs to 130,000 lbs
- Power Source: Hydraulic systems powered by an external pump
- Line Speed: Variable, depending on the hydraulic system's capacity
- Durability: Built to withstand harsh industrial environments
3. Manual Winches
Overview
Manual winches are the simplest and most cost-effective option. They are operated by hand, which makes them suitable for small-scale tasks like boat anchoring or trailer loading. Despite their manual operation, they can still handle moderate loads effectively.
Top 5 Applications
- Boating and Sailing: Manual winches are commonly used for hoisting sails and anchoring boats.
- Trailer Loading: They assist in loading heavy items onto trailers or trucks.
- Hunting and Camping: Manual winches are portable and useful for various outdoor activities.
- Home Garage: They help lift heavy objects or engines in DIY automotive projects.
- Small-Scale Construction: Used in tasks that don't require heavy machinery.
Typical Characteristics
- Load Limit: Typically up to 2,000 lbs
- Hand Crank: Requires manual effort to operate
- Portable: Lightweight and easy to transport
- Affordability: Cost-effective compared to powered winches
4. Air Winches
Overview
Air winches are a favorite in industries where electricity or hydraulic power is not readily available. They are powered by compressed air and are commonly used in mining, oil and gas, and other rugged environments. Air winches excel in situations where electrical equipment might pose a safety risk.
Top 5 Applications
- Oil and Gas Industry: Air winches are used in drilling operations and moving heavy equipment.
- Mining and Quarrying: They assist in material extraction and transportation in mining sites.
- Marine Offshore: Used for mooring and towing ships in challenging marine conditions.
- Construction: Air winches are employed in lifting and positioning heavy construction materials.
- Offshore Platforms: Vital for maintenance and equipment handling on offshore platforms.
Typical Characteristics
- Load Limit: Varies from 2,000 lbs to 100,000 lbs
- Power Source: Compressed air
- Durability: Designed to withstand harsh industrial environments
- Ex-proof Models: Available for use in explosive atmospheres
5. Confined Space Entry & Retrieval Winches
Overview
Confined space entry and retrieval winches are specialized tools designed for safety and precision. They are essential in industries like construction, where workers may need to access tight spaces for maintenance or rescue operations. These winches are designed to meet strict safety standards.
Top 5 Applications
- Construction and Maintenance: Confined space winches are used to lower workers into confined spaces safely.
- Rescue Operations: In emergency situations, these winches help retrieve individuals from confined spaces.
- Industrial Inspections: They assist in inspecting and maintaining equipment in tight spaces.
- Tank and Vessel Entry: Used in petrochemical and industrial settings for entry and exit from tanks.
- Utilities and Infrastructure: Confined space winches are used in the maintenance of sewers, pipelines, and tunnels.
Typical Characteristics
- Load Limit: Typically up to 310 lbs
- Cable Length: Varies but often up to 100 feet
- Safety Features: Equipped with features like automatic braking and emergency retrieval mechanisms
- Compact Design: Designed to fit into narrow spaces
6. Tie Down Winches
Overview
Tie down winches are essential for securing cargo during transportation. Whether you're hauling goods in a truck or securing equipment on a trailer, tie down winches keep everything in place. They are particularly important in ensuring safe and secure cargo transport.
Top 5 Applications
- Trucking and Transport: Tie down winches secure loads on flatbed trucks and trailers during transit.
- Boat Trailering: They help secure boats to trailers, preventing shifting during transport.
- ATV and Motorcycle Transport: Used to strap down recreational vehicles for safe transport.
- Construction and Equipment Hauling: Tie down winches keep heavy equipment in place on transport vehicles.
- Agriculture and Farming: Used in securing farm equipment and supplies during transport.
Typical Characteristics
- Load Limit: Ranges from 2,000 lbs to 10,000 lbs
- Ratchet Mechanism: Allows for easy tightening and releasing of straps
- Corrosion Resistance: Often made of durable materials to withstand outdoor conditions
- Versatility: Suitable for various types of cargo and tie-down applications
7. Winch Bars
Overview
Winch bars are handy accessories for winch operations. They provide leverage and control when tightening straps or cables. Winch bars are commonly used in conjunction with tie-down winches to ensure a tight and secure hold on cargo.
Top 5 Applications
- Trucking and Cargo Transport: Winch bars help truckers secure loads tightly for safe transportation.
- Flatbed Trailers: Essential for adjusting winch straps to secure various types of cargo.
- Vehicle Hauling: Used to tighten straps when transporting vehicles on trailers.
- Construction Sites: Winch bars assist in securing construction materials and equipment.
- Logistics and Warehousing: Involves securing pallets and goods for storage or transport.
Typical Characteristics
- Material: Often made of durable steel
- Handle Grip: Designed for comfort and control during use
- Compatibility: Fits most winches and tie-down systems
- Length: Typically around 34 to 40 inches
8. Winch Accessories
Overview
To get the most out of your winch, you'll need the right accessories. Winch accessories include items like snatch blocks, recovery straps, and winch covers. These accessories can enhance the performance and longevity of your winch.
Top 5 Accessories
- Snatch Blocks: Used to change the direction of the winch cable and increase pulling power.
- Recovery Straps: Provide extra strength for recovering stuck vehicles.
- Winch Covers: Protect the winch from the elements, extending its lifespan.
- Tree Savers: Used when anchoring winches to trees, preventing damage to the tree.
- Winch Line Dampener: Increases safety by absorbing energy in case of cable failure.
Typical Characteristics
- Material: Varies depending on the accessory, commonly made of durable materials like steel and nylon.
- Compatibility: Designed to work with specific winch models or universally adaptable.
- Safety Features: Some accessories include safety features like reflective strips for visibility.
9. Winch Cables
Overview
The strength and durability of your winch cable are critical. Winch cables come in various materials, including steel and synthetic options. Choosing the right cable for your winch and application is essential for safety and efficiency.
Top 5 Cable Types
- Steel Cables: Known for their strength and durability, ideal for heavy-duty winching.
- Synthetic Cables: Lightweight and easy to handle, suitable for off-road use.
- Wire Rope Cables: Combines the strength of steel with the flexibility of synthetic.
- Plasma Rope Cables: High-strength and lightweight, used in extreme conditions.
- AmSteel Blue Cables: Synthetic option with exceptional strength and no risk of splinters.
Typical Characteristics
- Material: Steel, synthetic fibers, or a combination of both
- Diameter: Varies based on the winch's capacity and application
- Length: Typically available in various lengths to suit different needs
- Safety Features: Some cables include safety hooks or thimbles for secure attachment.
10. Winch Remote Control Switches
Overview
Remote control switches add convenience to winch operations. They allow you to operate the winch from a safe distance, which is especially valuable in situations where precise control is necessary, such as vehicle recovery or marine operations.
Top 5 Applications
- Vehicle Recovery: Control the winch from a safe distance while recovering stuck vehicles.
- Boat Anchoring: Operate the winch remotely to raise or lower boat anchors.
- Off-Road Adventures: Stay safe while using the winch to navigate challenging terrain.
- Industrial Lifting: Control winches in construction and material handling operations.
- Marine Operations: Manage winches for tasks like lifting equipment on ships.
Typical Characteristics
- Wireless or Wired: Remote control switches are available in both wireless and wired options.
- Range: Wireless remotes typically have a range of up to 100 feet or more.
- Compatibility: Designed to work with specific winch models and brands.
- Convenience: Provide ease of operation and safety during winching tasks.
Wrapping It up:
That concludes our exploration of the top 10 most common types of winches and their applications. Remember, the right winch for your needs depends on factors like load capacity, intended use, and environmental conditions. You can find a wide selection of winches and accessories on GoVets to suit your specific requirements.
Signs That Your Winch Needs Replacement
Sometimes, maintenance alone may not be sufficient, and it's necessary to consider replacement. Signs that your winch may need replacement include repeated breakdowns despite regular maintenance efforts. If the device consistently fails to meet your load requirements or safety standards, it might be time for an upgrade. Obsolete technology can also be a compelling reason for replacement. Newer winches often come with advanced features, improved efficiency, and enhanced safety mechanisms that can outweigh the costs of continued maintenance and repairs. Additionally, changes in your operational needs, such as the need for higher load capacity or different functionality, may warrant replacing your winch with a more suitable model. Proper evaluation of your equipment's condition and alignment with your current requirements will help determine whether replacement is the best course of action.
Top 10 Signs That Your Winch Needs Replacement
Your winch is a workhorse, tirelessly lifting and pulling heavy loads, ensuring the smooth operation of your industrial processes, construction projects, or off-road adventures. However, like all machinery, these essential tools have a lifespan. Over time, wear and tear can take their toll, and the need for replacement becomes inevitable. In this section, we will explore the top 10 signs that indicate your winch is in need of replacement. These signs encompass a range of factors, from mechanical performance to safety considerations and changing operational needs. Recognizing these signs is crucial for maintaining the efficiency, safety, and reliability of your equipment.
Whether you're managing a fleet of winches in a construction site, utilizing hoists in manufacturing, or relying on a winch for off-road escapades, understanding these signs will empower you to make informed decisions about the future of your equipment. We'll delve into each sign in detail, providing insights into when and why replacement might be the best course of action. So, let's embark on this journey of equipment evaluation, where we decipher the signals your winch is sending, guiding you towards safe and efficient operations in the ever-evolving world of industry and technology.
- Frequent Breakdowns: If your winch experiences repeated breakdowns, despite regular maintenance efforts, it's a clear indicator that it may be nearing the end of its operational life. Frequent repairs can become costlier than investing in a new, reliable unit.
- Failure to Meet Load Requirements: When your winch consistently struggles to meet the load requirements of your operations, it's a sign that it's no longer up to the task. Upgrading to a higher-capacity model is essential for maintaining efficiency and safety.
- Safety Concerns: If your winch fails to meet safety standards or exhibits erratic behavior, it poses a significant risk to personnel and property. Safety should be a top priority, and replacing the equipment may be the only way to mitigate risks effectively.
- Obsolete Technology: Outdated technology can hinder productivity and efficiency. Newer winches and hoists often come with advanced features, improved energy efficiency, and enhanced safety mechanisms. These advantages can outweigh the costs of continued maintenance and repairs.
- Inadequate Speed or Control: If your winch lacks the speed or control needed for your operations, it can result in inefficiencies and delays. Modern units offer precise control and variable speed settings to optimize performance.
- Excessive Noise and Vibrations: Unusual noises or excessive vibrations during operation can be signs of internal wear or damage. These issues can compromise the integrity of the equipment and lead to more significant problems down the line.
- Corrosion and Rust: Severe corrosion or rust on critical components like cables, pulleys, or load-bearing parts can weaken the structure and compromise safety. Replacement may be necessary to ensure reliable performance.
- Inadequate Load Security: If your winch struggles to securely hold loads, it can jeopardize both your equipment and personnel. A reliable unit is essential for safe and efficient load handling.
- Changing Operational Needs: Changes in your operational requirements, such as the need for higher load capacity or different functionality, may necessitate replacing your existing winch with a more suitable model. Ensure your equipment aligns with your evolving needs.
- Excessive Wear and Tear: Visual inspection can reveal signs of excessive wear and tear, such as frayed cables, worn-out gears, or damaged structural components. These are clear indications that your equipment is reaching the end of its service life.
Properly evaluating these signs and conducting a thorough assessment of your equipment's condition will help you make an informed decision regarding replacement, ultimately enhancing productivity, safety, and operational efficiency.
Maintenance of Winches and Hoists
Proper maintenance is vital to ensure the longevity and safety of winches and hoists. Regular inspection and upkeep tasks include lubrication of moving parts, checking for wear and tear, and verifying the integrity of cables or ropes. For electric winches, electrical connections should be inspected for signs of corrosion or damage.
Scheduled maintenance should be performed according to the manufacturer's recommendations, taking into account the frequency of use and environmental conditions. This may involve more in-depth inspections, such as load testing, and the replacement of worn components.
Winches and Hoists Maintenance
Proper maintenance is vital to ensure the longevity and safety of winches and hoists. Regular inspection and upkeep tasks include lubrication of moving parts, checking for wear and tear, and verifying the integrity of cables or ropes. For electric winches, electrical connections should be inspected for signs of corrosion or damage.
Scheduled maintenance should be performed according to the manufacturer's recommendations, taking into account the frequency of use and environmental conditions. This may involve more in-depth inspections, such as load testing, and the replacement of worn components.
Signs of Well-Deserved Maintenance for Winches and Hoists
Several signs indicate that your winch requires maintenance. These include unusual noises during operation, such as grinding or squeaking, which may indicate worn-out components. Slow or jerky movement can signal issues with the winch or hoist's motor or gearbox.
Frayed cables or ropes, visible rust or corrosion, and loose fasteners are clear signs of wear and tear that require immediate attention. Any irregularities in the control system, such as unresponsive buttons or switches, should also prompt maintenance.
Top 10 Signs of Maintenance and Replacement for Winches and Hoists
Introduction:
Your winch is a critical component of your operations, whether in heavy industry, construction, or recreational use. Keeping these devices in optimal condition ensures safety, efficiency, and longevity. This section explores the top 10 signs that indicate the need for maintenance and, in some cases, replacement of your winch or hoist.
Signs of Needed Maintenance
- Unusual Noises: During operation, if you hear grinding, squeaking, or other unusual noises, it's a sign that something isn't right. These sounds may indicate worn-out components or insufficient lubrication.
- Slow or Jerky Movement: If your winch exhibits slow or jerky movement, it can signal problems with the motor, gearbox, or lubrication. Proper maintenance can often rectify these issues.
- Frayed Cables or Ropes: Visual inspection is crucial. Frayed cables or ropes compromise safety and performance. Replace them promptly to prevent accidents.
- Visible Rust or Corrosion: Rust and corrosion weaken the structural integrity of the equipment. Regularly inspect and address these issues to prevent further damage.
- Loose Fasteners: Vibrations and heavy loads can cause fasteners to become loose. Tighten them to ensure the winch remains secure and stable.
- Irregular Control System: If buttons or switches become unresponsive or erratic in their function, it's a clear indication of control system issues. Address these promptly to maintain control over your equipment.
- Overheating: Excessive heat during operation can lead to motor damage. Monitoring the temperature and addressing overheating issues is crucial for preventing costly repairs.
- Fluid Leaks: For hydraulic winches or hoists, fluid leaks can indicate problems in the hydraulic system. Address leaks promptly to prevent loss of hydraulic pressure and reduced performance.
- Excessive Vibrations: Unusually high vibrations can indicate misalignment or damaged components. Identifying and rectifying the source of vibrations is essential for equipment safety.
- Inadequate Load Security: If your winch struggles to securely hold loads or shows signs of slipping, it's a clear sign of maintenance needs. Proper load security is essential for safety.
Regular maintenance helps address these signs promptly, ensuring your winch remains in optimal condition. However, there are instances when maintenance alone may not suffice, and replacement becomes necessary, as we'll explore in the following section.
History of Winches and Hoists
The history of winches and hoists dates back thousands of years. Early civilizations, including the Egyptians and Greeks, developed rudimentary hoisting systems using simple machines like pulleys and ropes. These innovations laid the foundation for more advanced hoisting mechanisms.
In the industrial revolution, steam-powered winches and hoists became prominent, transforming industries like mining and construction. The 20th century saw the advent of electric and hydraulic winches and hoists, further enhancing their versatility and power.
Today, modern winches and hoists incorporate cutting-edge technology, offering precise control, safety features, and increased load capacity. They have become indispensable in various sectors, from manufacturing and shipping to rescue operations and entertainment industries.
The Rich History of Winches and Hoists: From Ancient Pulleys to Modern Powerhouses
The history of winches and hoists is a journey through time, showcasing humanity's ingenuity and determination to conquer the challenges of lifting heavy loads. Dating back thousands of years, these essential tools have evolved from rudimentary systems to sophisticated machinery that powers various industries today.
Ancient Beginnings:
The origins of winches and hoists can be traced to ancient civilizations such as the Egyptians and Greeks. These early innovators developed rudimentary hoisting systems using simple machines like pulleys and ropes. These inventions were pivotal in simplifying tasks that required lifting or lowering heavy objects. Pulleys, in particular, played a significant role by distributing the load's weight across multiple ropes, making it easier to manage.
The Industrial Revolution:
Fast forward to the industrial revolution, and winches and hoists underwent a remarkable transformation. Steam power became the driving force behind the development of these tools, leading to the emergence of steam-powered winches and hoists. This technological leap had a profound impact on industries like mining, construction, and manufacturing.
Steam-powered winches and hoists revolutionized the mining sector by enabling the efficient extraction of valuable resources from deep within the Earth. In construction, these robust machines facilitated the lifting and placement of heavy materials, accelerating the pace of large-scale building projects.
The Electrifying 20th Century:
The 20th century brought yet another wave of innovation to winches and hoists. The development of electricity and hydraulic power sources ushered in a new era of versatility and power. Electric winches and hoists offered precise control and efficiency, making them ideal for various applications, from manufacturing assembly lines to entertainment industry setups.
Hydraulic winches and hoists, on the other hand, harnessed the power of pressurized fluids to lift and lower heavy loads. This technology was particularly valuable in scenarios where electricity was impractical or hazardous, such as marine operations.
Modern Marvels:
Today, modern winches stand as true marvels of engineering. They incorporate cutting-edge technology and materials, offering enhanced precision, safety features, and significantly increased load capacities. These tools have found their place in a wide array of industries, contributing to efficient and safe operations.
Electric winches, for instance, feature advanced control systems that allow operators to fine-tune load movement with remarkable accuracy. This level of control is critical in applications such as material handling in manufacturing facilities or raising and lowering stage equipment in the entertainment industry.
Hydraulic winches, on the other hand, continue to excel in marine operations, where their durability and reliability are essential for tasks like lifting and lowering anchors or recovering submerged objects. They are also favored in construction projects that demand robust lifting capabilities.
Innovations in materials, such as high-strength steel cables and synthetic ropes, have further enhanced the performance and safety of winches and hoists. These developments have enabled these tools to take on even more challenging tasks while minimizing the risk of accidents.
In conclusion, the history of winches and hoists is a testament to human creativity and engineering prowess. From the earliest pulleys and ropes to the powerful electric and hydraulic machines of today, these tools have played a vital role in shaping industries and pushing the boundaries of what's possible. As we look to the future, it's clear that winches and hoists will continue to evolve, driving progress and efficiency across diverse sectors.
Conclusion
Winches and hoists are indispensable tools that have evolved over centuries to meet the needs of various industries. From their humble beginnings with pulleys and ropes in ancient civilizations to the sophisticated electric, hydraulic, and manual systems of today, these devices play a crucial role in lifting heavy loads and ensuring efficient operations.
Regular maintenance is essential to keep winches and hoists in optimal condition. It includes tasks like lubrication, inspection for wear and tear, and adherence to manufacturer recommendations. Signs of needed maintenance include unusual noises, slow or jerky movement, frayed cables, corrosion, and control system irregularities.
However, there comes a time when maintenance alone may not suffice, and replacement becomes a viable option. This decision can be prompted by recurring breakdowns, outdated technology, or changing operational needs. Replacing old or inefficient winches and hoists with modern counterparts can enhance productivity, safety, and overall efficiency.
In the ever-evolving world of industry and technology, winches and hoists continue to adapt and innovate, contributing to safer and more efficient operations across diverse sectors.